Symptoms of a bad fuel pump
What are the symptoms of a bad fuel pump
If your engine won’t start, takes too much cranking to start or your engine stalls, you may have a bad fuel pump or you may have a fuel pump wiring issue caused by a corroded connection or ground or a bad fuel pump control module. The point is, perfectly good fuel pumps get replaced because people don’t always know the symptoms of a failing fuel pump or do the proper testing before replacing the pump.
Symptoms are different between electric and mechanical fuel pumps
Older cars equipped with carburetors usually have mechanical fuel pumps driven by the camshaft and a follower pin. However, newer cars with fuel injection have electric fuel pumps located in the fuel tank and they have different failure symptoms than a mechanical fuel pump. I’ll go through the most common symptoms of a bad fuel pump for fuel injected vehicles.
Engine cranks a long time before it fires up is sign of a bad check valve in the fuel pump
What we’re talking about here is an engine that must crank for 2-8 seconds before it actually fires up after sitting overnight or for several hours. You know it’s lack of fuel because the engine starts if you spray or pour fuel into the intake or your fuel pressure gauge shows too low a fuel pressure or even no fuel pressure.

Turbine style fuel pump showing the turbine, motor and check valve
What the check valve does
The check valve prevents fuel from draining back into the tank once you shut off the engine. It also retains most of the fuel pressure that was built up by the pump so you’ll instantly have both fuel and pressure when you try to start the engine.
What’s the fix for a bad fuel pump check valve
The check valve is not available from the dealer as a separate item so most shops replace the entire fuel pump. Some car makers make that easy by incorporating a removable access cover in the back seat. Remove the cover, disconnect the power and fuel lines, remove the retaining ring and lift out the old pump. Then reverse to install.
Other car makers make it much harder, requiring you to disconnect the fuel tank filler hose and all the emissions devices and then lower the tank to access the fuel pump. That’s a LOT of work just to replace a very small check valve.
Even if your car has the access cover, fuel pump replacement isn’t cheap. Depending on whether you buy an OEM or aftermarket fuel pump module, you can expect to pay anywhere from $300 to $800 to replace the entire fuel pump module to correct a stupid little check valve.
S.U.R.&R. makes an add on check valve
S.U.R.&R. came up with a more cost effective solution that’s MUCH easier. The add-on CKV5 & CKV7 check valves install right into the high pressure fuel line OUTSIDE THE TANK and prevent gas and pressure from bleeding off.
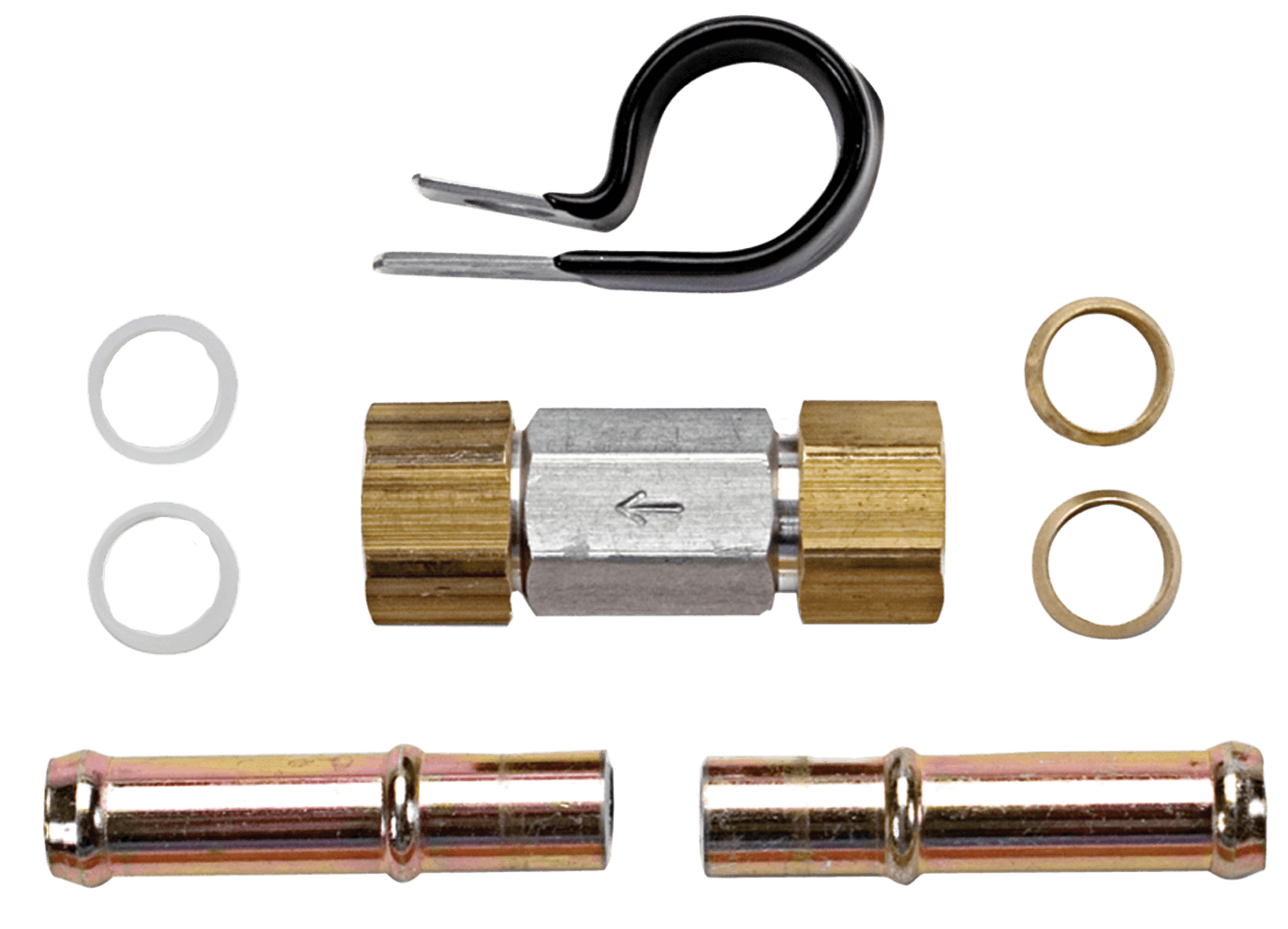
S.U.R.&R. add on fuel pump check valve #CKV5
The check valves come in two sizes; CKV5 for 5/16” lines and CKV7 for 3/8” lines.
How to install S.U.R.&R. CKV5 and CKV7 check valves
The S.U.R.&R. check valves work on RETURN style fuel systems. You can spot those systems because they have a pressure line running up to the fuel rail and a return line after the fuel pressure regulator. The check valves should not be installed on return-less fuel systems.
To install, simple depressurize the fuel system by removing the fuel pump fuse and starting and running the engine until it stalls. Then cut the fuel line as close the tank as possible. Wear protective gloves and eye protection and be prepared to catch any remaining fuel in the lines.
If you have steel fuel lines, use the metal compression fittings. If you have nylon lines use the nylon compression fittings.
Install the check valve with the arrow pointing towards the engine. Reconnect the fuel pump fuse and start the engine. Check for leaks.
Click here for more information on the S.U.R.&R. add on fuel pump check valve.
Engine will start only if you add fuel is a symptom of a bad fuel pump
A bad fuel pump can fail to run at all, may run but not pump the correct fuel volume, or it can run buy fail to build adequate fuel pressure. Or, the fuel pump may deliver the correct volume and pressure buy only after the engine has been cranking for several seconds. That would indicate a faulty check valve in the fuel pump that allows fuel rail pressure to leak down after the engine is shut off. On cold restart, there’s no residual fuel pressure in the lines and the pump has to run longer to build fuel pressure.
Engine sputters at high speed is a symptom of a bad fuel pump
This would be an indication that the fuel pump can’t meet the fuel volume or pressure demands of the engine when its running at high RPMs.
Loss of power when accelerating is a symptom of a bad fuel pump
Low fuel pressure or low fuel volume can cause a loss of power on hills or during period of heavy or rapid acceleration. In other words, the fuel pump can’t keep up with fuel demands when the engine is under heavy load.
Engine surges is a symptom of a bad fuel pump
In this case the engine speed increases or decreases without any driver input. DIYers mistakenly blame this on a clogged fuel filter, but the fuel filter is usually not the cause of surging. Clogged fuel filters usually don’t cause an erratic symptom because they’re either clogged or not clogged.
What causes fuel pump failure?
• Driving the vehicle when low on gas—Fuel pumps get hot and car makers rely on gas in the tank to cool the electric motor. When you run the vehicle constantly near empty, the fuel pump runs hot and wears out prematurely. Then, when you finally add gas, it stirs up whatever debris was in the tank and it’s sucked into the pump.
• Bad fuel—This is the number one cause of fuel pump failure. Ethanol fuel goes bad after 30-days. The alcohol separates from the gas and falls to the bottom of the tank. Since alcohol is hygroscopic, it absorbs any moisture in the tank. The water laden alcohol causes tank corrosion and that corrosion settles at the bottom of the tank and clogs the pump filter, called a “sock”. The moisture can also react with air to form bacteria or fungus which also clogs the sock. In addition to internal corrosion, you can introduce dirt every time you remove the gas cap and insert the nozzle.
• Water in the gas—Leaving old gas in your vehicle causes water to build up.
• Corroded electrical connections—electric fuel pumps use a lot of power, so they require good electrical power and ground connections. I’ll never understand why car makers place the ground connection under the vehicle where it’s exposed to road salt conditions, but they do. Once a power or ground connection gets corroded, it creates extra resistance which increases amperage draw while reducing voltage. That overheats the motor windings and causes them to deteriorate.
• Not cleaning the fuel tank before replacing a fuel pump—Flushing and cleaning the tank with the proper detergent is mandatory when replacing a fuel pump. In most cases you can’t do this at home. Take the tank to a radiator repair shop and pay them to steam clean it.
If you skip this step thinking that the filter sock on the new fuel pump module with strain out the debris and contaminants, think again. Most sock strainers are designed to catch particles between 50-100 microns. But a fuel filter catches particles as small as 10 microns. So the larger debris will get sucked right into the pump and wear it out before the fuel even reaches the fuel filter. In addition, the sock is very small and has a limited ability to capture debris.
• Next, failure to filter the fuel you removed from the tank is another huge mistake. That fuel has come in contact with dirt and road debris and any crud that was in the buckets you used to store it while you worked on the tank. If you simply pour it back into the tanks, you’re adding all that crud.
How to diagnose a bad fuel pump
To properly diagnose a fuel pump you’ll need a fuel pressure gauge, digital voltmeter, and, in some cases, a digital scope.
First conduct a fuel pressure test
Connect the fuel pressure gauge to the test port or a testing location
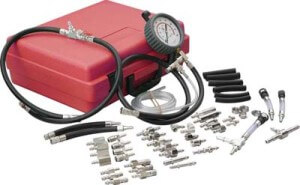
A fuel pressure test gauge kit includes all the fittings you need to connect to your vehicle. But or rent one. BETOOLL Pro Fuel Injection Pressure Tester Kit Gauge
somewhere on the fuel line. Find the factory specs in a shop manual. Turn the key to ON several times (engine off) to build pressure and see if the fuel pump reaches the specified pressure. If it does, then take the vehicle for a test drive to make sure it maintains that pressure when under load.
Then conduct a fuel volume test
A bad fuel pump can sometimes deliver the right pressure but not the proper volume. Activate the pump and measure the amount of fuel it delivers in 30-seconds. Then compare the fuel delivery volume to the car maker’s specs. If it fails to deliver the correct volume, replace the bad fuel pump.
Perform a fuel pump leak down test
If the engine requires an extended crank time when cold, test for check valve fuel leak down. Repeat the test above to build pressure. Then leave the gauge attached and leave the vehicle for several hours or overnight. If the fuel system loses more than 5-10-psi. the check valve if faulty and the fuel pump must be replaced.
Test for good power and ground
On older fuel injected vehicles, test for the presence of battery power at the fuel pump connector when turning the key to ON. Then check for good ground. However, newer vehicles with return less fuel systems, don’t provide a constant 12-volts to the pump. Instead, they use a fuel pump driver module that pulses power to the pump to help regulate pressure and volume. If your vehicle has a fuel pump driver module and you don’t read 12-volts at the connector, don’t assume the driver module is bad. Instead, test with a scope.
Test for voltage drop
Voltage drop is the least understood electrical concept, yet it’s also the most important test you can do. Resistance in the circuit reduces voltage and increases current draw. As mentioned earlier, this reduced voltage damages the pump. Learn how to do a voltage drop test and perform this before replacing a suspect fuel pump. Almost 50% of all warranty returned fuel pumps are good and where needlessly replaced due to faulty testing.
Scope test
Electric motors work by connecting power to a segmented commentator. As these motors wear, a bad winding or bad commutator segment can cause fuel pressure and delivery problems. Sometimes the only way to isolate the problem is to use a digital scope to spot the cyclical voltage change as the brushes wipe against the bad commutator segment.
Is it a bad fuel filer or a bad fuel pump?
When a fuel filter is clogged with debris, it can flow enough fuel at low engine RPMs, but not when the engine is under load. DIYers often blame a bad fuel filter for rough idle or misfires at idle speeds, but that’s rarely caused by a bad fuel filter.
Fuel filters rarely cause idling or misfire problems at low engine RPMs! If they’re that clogged that they can’t deliver enough fuel at idle, they generally can’t even provide enough fuel to start the engine in the first place.
If you have an externally mounted fuel filter and you’re having engine problems under load, changing the fuel filter is an inexpensive and fairly easy place to start. Unfortunately, many car makers install the fuel filter inside the fuel tank.
What is a fuel pump module
An electric fuel pump is basically an electric motor with a rubber
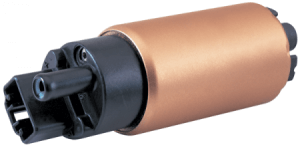
Fuel pump
impeller located on the end of the motor shaft. The motor spins the impeller and it pumps fuel up to the injectors. In some vehicles, the fuel pressure regulator is located at the engine. In that case, the pump outputs a constant volume of fuel at a high pressure. The fuel pressure regulator bleeds off the excess volume and pressure and that fuel returns to the tank via a return line.
Later model vehicles incorporate the fuel pressure regulator
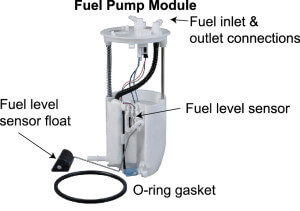
The fuel pump module housing contains the fuel pump, pulsator, filter sock, fuel level sensor, float and float arm, inlet and outlet connections, and springs to keep the unit at the bottom of the tank
right at the pump. This eliminates the return line and these systems are known as returnless fuel systems.
In addition to a pressure regulator, car makers also include a noise reduction component called a pulsator. This unit acts like a mini shock absorber to reduce fuel pump noise.
Finally, many car makers not incorporate a fuel filter and the fuel level sending unit into the fuel tank right in line with the fuel pump. A fuel pump module contains the fuel pump, pulsator, fuel level sending unit, and a fuel filter (if equipped). You can replace just the fuel pump, but that’s a really bad idea. Here’s why:
To remove the fuel pump module, you usually have to empty and drop the fuel tank. Then you have to remove the entire fuel pump module. Once you remove it, you have to disassemble the fuel lines running into and out of the pump. These lines can be crimped or simply pushed together using O-rings to seal the tubing. Most DIYers think they can just reuse the O-rings and crimp rings, and that’s where you get into trouble. These pumps put out a lot of pressure and any leak in the tubing can cause trouble. The only thing worse than draining a dropping a fuel tank once, it to have to drain and drop it repeatedly. That’s why most shops won’t even consider replacing just the fuel pump and instead replace the entire fuel pump module.
What is a fuel pump driver module?
In the early fuel injected engine designs, the fuel pumps were designed to run at full speed and full pressure the entire time the engine was running. As I
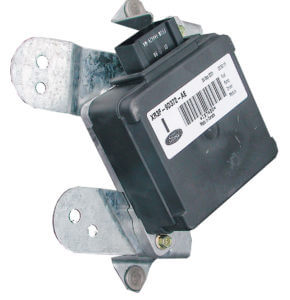
Fuel Pump Driver Module
described earlier, the fuel pressure regulator bled off the unneeded pressure and either returned it to the fuel tank or bled off the pressure right in the fuel tank.
Late model fuel injected vehicles use an entirely different fuel pump delivery strategy. Instead of running the fuel pump at full speed, full time, these vehicles employ a fuel pump driver module along with a fuel rail pressure/temperature sensor to run the pump only as needed.
The fuel system control strategy is a software program stored in the PCM. Using accelerator pedal position information and fuel rail pressure/temperature inputs, the PCM can direct the fuel pump driver module to regulate fuel pump speed to match engine needs.
The PCM commands a duty cycle command to the fuel pump driver module method where it pulses voltage to the fuel pump, resulting in a variable speed fuel pump operation. In this type of system, the fuel pump runs only fast enough to meet the engine’s fuel needs. This method conserves power, which results in better MPG.
Unfortunately, many DIYers misdiagnose these systems due to the varying voltage going to the fuel pump. If you use a digital voltmeter to check voltage to the fuel pump at idle, you may suspect a bad fuel pump or electrical problem where there is none. Here’s how you can get fooled. The engine doesn’t need as much fuel at idle, so the fuel pump driver module pulses power less often to the fuel pump. Since a digital voltmeter can’t track rapid voltage changes, what you see on the screen is an average of the voltage, and that can make you think the fuel pump isn’t getting the proper voltage.
The only way to properly diagnose these systems is to use a scan tool with live data and a scope that can track the voltage pulses.
©, 2015 Rick Muscoplat
Posted on by Rick Muscoplat